Distribution center out of space?
In 2017, warehouses and distribution centers are under increasing pressure to adapt to meet the growing e-commerce demand.
Space is limited and opening new distribution centers may not always be an option. In this environment, it is important to take a hard look at current operations to see areas that could be more efficient.
If not yet at the stage to expand facilities, companies will have to find another solution. This typically means condensing current operations.
For Lance Crosby, President of Northern Sales Company, Inc., this was a clear first step.
“You need to focus on compressing open space. From unused pallet rack pick locations to how wide the isles and the type of equipment you’re running.”
For a company facing the challenge of limited space, it is important not to overlook simple solutions that could add up to significant cost savings. For instance, something direct such as changing equipment to narrow or very narrow isle trucks could cut aisle widths in half, opening up space for entire new isles to maximize the current space.
Automated storage and retrieval systems can also be a solution and allow denser storage where large open isles are not required, but the cost of implementing these systems can make them illogical for some operations.
“Cost is a very important factor. There are certainly automated systems out there, but they can run millions of dollars,” said Mr. Crosby.
Something not always properly considered is the maintenance costs of these systems. Outside technicians must perform regular maintenance and repairs, and current warehouse maintenance crews need training to be able to handle typical problem solving. This can make realizing a significant ROI difficult, especially for smaller operations. Utility bills also greatly increase as the systems are constantly running and drawing power.
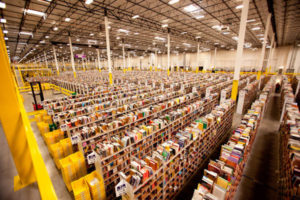
The benefits of a storage layout audit
Another area to consider when evaluating warehouse space efficiency is how a company is addressing its dead space. This could be the space between pallet racks where pickers would not be able to reach products, or un-used space along walls that could be utilized; anywhere there is room for storage, but because of the current layout, it is not being leveraged.
Performing a storage layout audit could reveal areas for companies that they did not realize could be redesigned, allowing them to make the most of their current space and delaying a costly expansion. Growth is a great problem to have, but it makes sense to focus first on making the most of current space before looking outward.